Blog
Unlock Engineering Insights: Explore Our Technical Articles Now!
Driven by Code: The Software-Defined Vehicle Podcast
Explore the World of Software-Defined Vehicles – Tune in to Driven by Code!
eBooks, Whitepapers, and Case Studies
Unlock a Wealth of Knowledge – Explore Our eBooks, Whitepapers, and More!
Webinars and Videos
Stay Informed and Inspired – Watch Our Webinars and Videos Now!
Process & Automation
Systems & Software Dev
Verification & Validation
Software Quality & ASPICE
Promote the order, control, and proper flow from the definition
of requirements through design, development, testing, and verification.
Get Started Today!

Need ASPICE Consulting Contact us TODAY!
Software Quality & ASPICE
Automotive technology and supply networks are becoming more complex; your process assessment doesn’t have to be! This increases the possibility of failure triggered by a system design error or software implementation issue. With passenger and public safety at risk, prudent organizations will take advantage of standards such as ASPICE to ensure that products will be built on a solid foundation and an irreproachable process.
ASPICE provides a framework for evaluating and improving the development and implementation of software and related systems embedded in motor vehicles. This ASPICE framework can be extended to hardware engineering and mechanical engineering using processes through which requirements are defined and designs are developed.
ASPICE promotes order, control, and proper flow from the definition of requirements through design, testing, and verification.
ASPICE can reduce development costs. Using the standard’s processes, errors and defects will be found earlier in development when they are less costly to correct. Also, as the organization learns and standardizes internal processes, there is an opportunity to work more efficiently through avoidance of repeated errors, reuse of gained knowledge, and consistent approaches to the work.
LHP’s Team of functional safety experts have decades of experience in process management, assessment, and requirements gathering that is designed to help lead your team through value-added approaches for process assessments and system improvements.
Our approach of an ASPICE assessment and gap analysis, recommended action plan, and full implementation allows your organization peace of mind knowing that LHP will guide you through every step of the process.
When used properly, ASPICE offers:
-
Improved Quality and Reliability
-
Better Requirements Manageability
-
Reduction of Risk
The changes in the update from ASPICE 3.1 to 4.0
ASPICE was created, much like other software quality systems, to aid engineers and developers in managing the increasingly complex world of embedded controls and software. ASPICE 4.0 represents a continuation of that effort, with clarification of requirements and streamlining among its goals.
The change between ASPICE 3.1 and 4.0 that would impact organizations the most is the addition of hardware engineering and machine learning process groups. This expands the applicability of the standard to address the entire system lifecycle, by including hardware, and provides regulation for the new aspects of machine learning.
ASPICE 3.1 process reference model has been updated to the following ASPICE 4.0 process reference models:
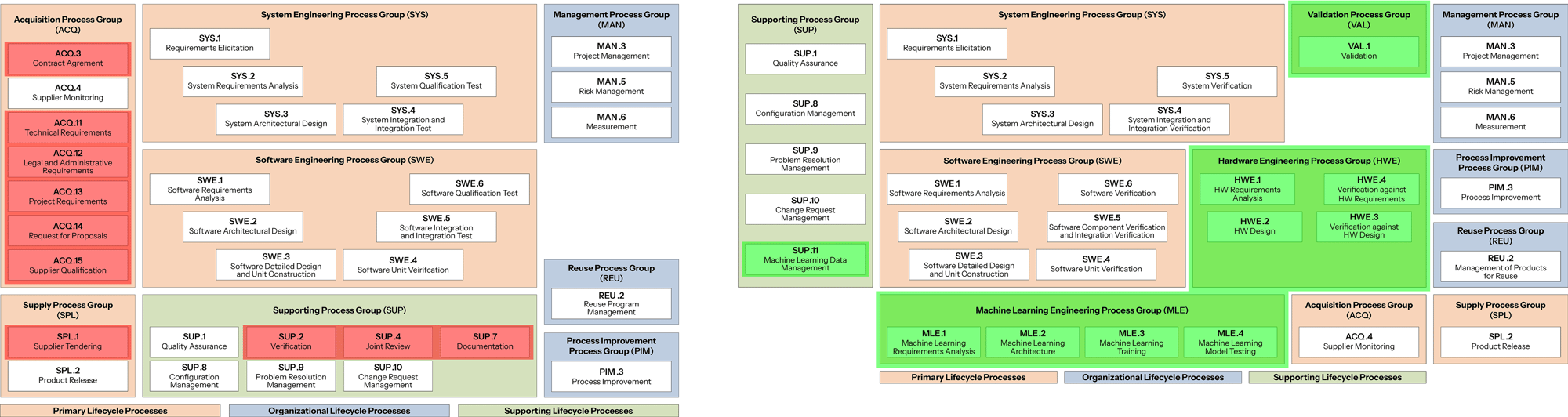
ASPICE Offerings
-
Assessment
Input: Understand the customer goals and objectives based on existing processes.
Output: Assessment report and/or Functional Safety implementation plan, project plan tailored to your needs with prioritized list of actions based on assessment.
-
Trusted Process
Input: Functional Safety implementation plan, business needs
Output: Certified or compliant corporate processes for implementation of Functional Safety tailored to your needs
-
Tool Selection & Qualification
Input: Functional Safety implementation plan, current development toolchain, existing design portfolio, product line roadmap, business needs and constraints
Output: Functional Safety compliant framework, integrated toolchain, for product development that aligns with overall goals and engineering department workflow
-
Training
Input: Mapping of existing skills related to business needs, product line roadmap
Output: Training on safety-related processes or tools to close the gaps and accelerate the development team
-
Functional Safety Product Design & Development
Input: Business needs and stakeholder/product requirements
Output: Functional Safety certified/compliant ECUs (Systems, Hardware, Software, Design and Test)
-
Safety & Project Management
Input: Assessment, Work Scope, Project Management
Output: Schedules, budget, plans to achieve Functional Safety
-
Standards Comparative Analysis
Input: Applicable business standards, product roadmap
Output: Analysis report and implementation plan
-
Functional Safety Verification & Validation
Input: Systems, software, hardware requirements, and business processes and tools
Output: Verification and validation of systems, including the development of test equipment, and processes documentation (Functional Safety / ASPICE / DO-178 or other)
-
Safety Analysis
Input: Product requirements and design
Output: Safety analysis from concept to production (i.e. HARA, FMEDA, FHA, FTA, etc.)
ASPICE Blog Post
5 min read
The Role of ASPICE in Systems and Software Development
Apr 9, 2024 by Steve Neemeh
6 min read
An Introduction to Verification and Validation Testing for ADAS
Feb 16, 2021 by Steve Neemeh